How Döpke solves the digitization of its product portfolio faster and more innovatively with 3D production
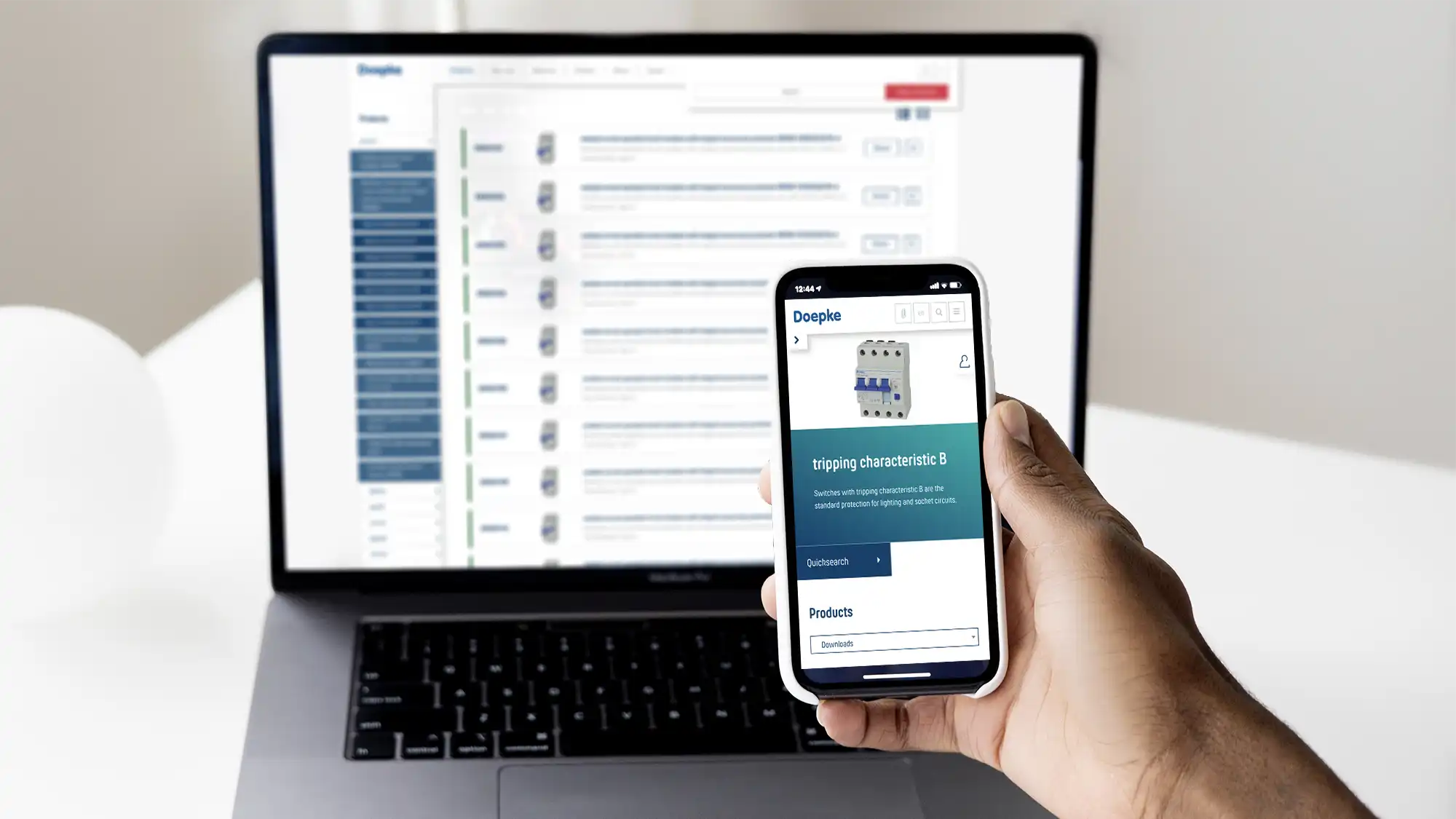
Challenge - efficient combinations for numerous product variants
Döpke Schaltgeräte GmbH is an internationally active manufacturer of residual current protection technology. The traditional medium-sized company from the north in East Frisia was one of the world's pioneers in the development of residual current circuit breakers, generally known as FI switches. Today, Döpke sells a variety of different models and various other products in the area of residual current protection.
As a result of the growing variety of models and different labeling requirements, it became more and more complex over time to display the switches uniformly.
In an expensive and lengthy process, each switch model had to be presented individually. New switch variants could not simply be integrated, but had to be photographed from scratch every time.
In search of more efficient alternatives to traditional product photography, Döpke finally decided to work with RenderThat.
Solution - 3D product visualization with CGI
As an expert in CGI pipelines and scalable product presentations, RenderThat should first develop an efficient solution for creating 2000 different computer-generated product visualizations.
Compared to traditional photography, the intended CGI solution should significantly simplify and accelerate future adjustments to the product range and the inscriptions.
RenderThat developed corresponding “digital twins” on the basis of 23 different switch designs. Döpke provided the original switches and explained their special features.
One focus was on the printing area for lettering and marking. Critical information such as item name, design, instructions for use and other important safety symbols would later be placed on this surface.
In the course of the project, RenderThat developed a number of individual solutions to be able to respond to specific challenges. The result was an efficient system that enabled automatic file adjustment, the storage of print data and finally the visualization of the products.
Different fonts and formats within the master data proved to be a particular challenge. These first had to be adjusted manually before the actual automation process could start. RenderThat and Döpke worked closely together throughout the entire period and were therefore able to successfully implement even short-term changes.
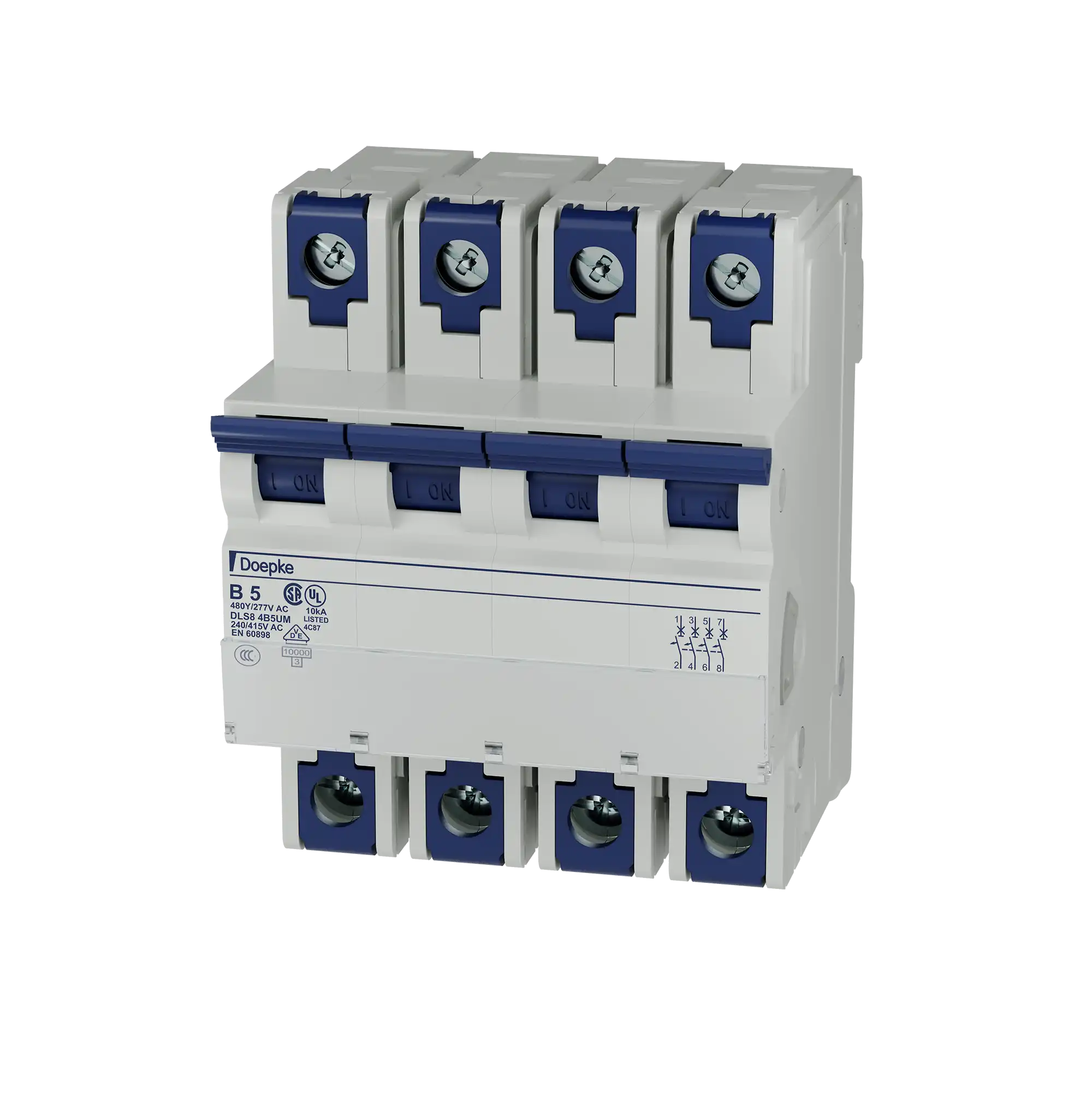
Result - 3D visualization as an automated product pipeline
Through the effective use of powerful CGI technology and the meticulous work of its team, RenderThat was able to faithfully reproduce all 23 switch types in detail and prepare them for the automation process within a very short period of time.
The developed CGI pipeline was based on the product database, which contained the individual product specifications.
In another automated process, RenderThat created the various printing plates (printing schemes) and combined them with already completed product visualizations. In this way, new visualizations were created within a few seconds.
Thanks to this process, Döpke received over 2,000 individual images of his products within a very short period of time. The impressive result: Even with the first delivery, the error rate was less than 1%. RenderThat corrected the few remaining inaccuracies immediately afterwards and was thus able to deliver Döpke a final product of the highest level.
Before working with RenderThat, Döpke had to extensively stage each and every one of his numerous switch models for product photography.
Due to the time interval between the introduction of new products, the corresponding photo setup had to be rebuilt again and again. As a result, the camera perspective and lighting were never really identical, which is why the resulting images did not completely match each other. A uniform visualization of the products was therefore impossible. This previous process was not only inefficient, but also cost the company a lot of time and money.
Thanks to RenderThat's CGI production, Döpke now has digital renderings of its designs and can digitally adapt all labels quickly and easily.
With the RenderThat CGI pipeline, identical results can be achieved even over a longer period of time. This not only saves resources, but also enables a modern, uniform product presentation.
Through cooperation with RenderThat, Döpke is using the benefits of digitalization specifically to further develop its product presentations. The result of this collaboration once again demonstrates the advantages of CGI production compared to product photography. Döpke can now flexibly digitally manage its products and implement the complex labeling requirements of the electrical industry even more effectively. The company can present all switch models directly to its B2B customers in the form of product visualizations.
Döpke and RenderThat are continuing their successful cooperation. For example, RenderThat is currently working on expanding the CGI pipeline and new areas of application. It is already clear that in the near future, Döpke will be able to present its products even faster and more extensively than before.
With RenderThat's CGI production, Döpke is successfully focusing on digital innovation. The company can now present its products more consistently, manage them much more easily and reduce costs in the process.
Make yours Product digitization more efficient
We help companies digitize product portfolios with hundreds of items. Our workflows are tailored to your company and ensure maximum output with minimal effort.
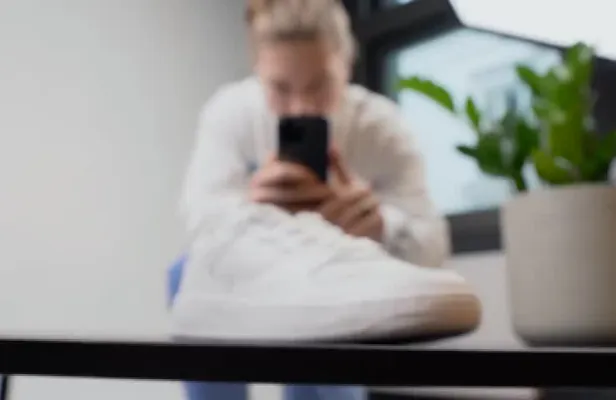